
The Challenge of
Nai Monozukuri
Koromo means “clothing,” and our Koromo Research Department is where our monozukuri’s roots lie. Here we make our own raw materials, yarn, fabric, designs, plans, colors, patterns, and even printing templates. There may be no other clothing company that does all this themselves, but we have no choice—the things we want don’t exist anywhere else. This is how we came up with our philosophy of nai monozukuri: creating things that don’t exist (nai mono), but feel like they should.
We love garments that are frank and to-the-point—that make the power of their raw materials tangible. We visit artisanal workshops all over the world to learn from traditional costumes. We also seek clothing with a certain elegance and refinement. Above all, we adore clothes that simply feel good to wear. You might say that we’re pursuing the rarest, purest, and most extreme examples of the form. The challenge of nai monozukuri is never-ending.

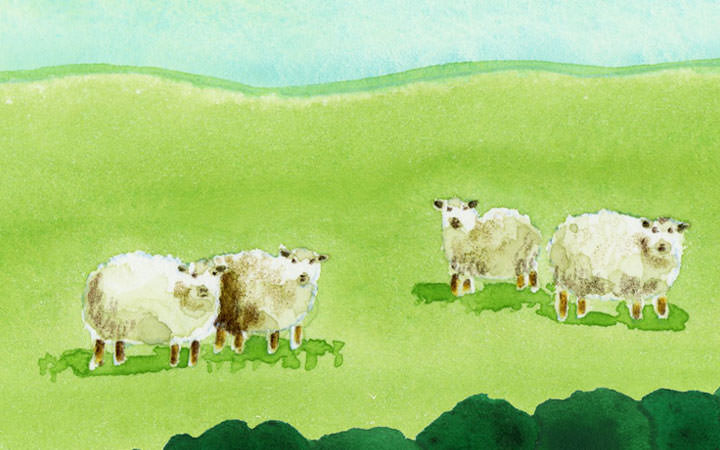
Wool
Many different kinds of wool are used in clothes:
Shetland, Merino, Arles, Alpaca, Cashmere . . . Every
variety is unique in its own way, reflecting the kind of
animal it grows on and the environment they live in.
For
example, Shetland Island is cold and windy, so the sheep
there have stiff, durable wool to protect them from the
harsh natural conditions. Shetland wool has a supple
elasticity and gloss that is second to none. That’s why
genuine Shetland wool from sheep living on the island is
the only raw material we accept for tweed jackets and
Shetland knits.

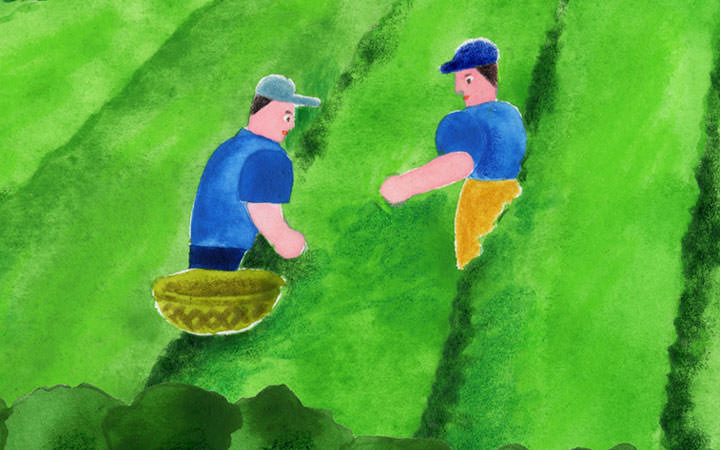
Ai Indigo
It was probably inevitable that our pursuit of perfection
would eventually lead us to 100% natural Ai indigo. The
colors it imparts to clothing, which also depend on local
climate and environmental conditions, have a depth and
complexity that chemical dyes could never replicate.
The
variety traditionally cultivated in Japan is called
tade-ai, or Persicaria tinctoria. It takes around a year
to complete a single batch—to grow a field full of it
which is then harvested, fermented, and prepared for the
dyeing process. We cultivate our Ai Indigo with great,
great care.
Sowing: March
Setting:
April
Cultivation: May–June
Harvest: Late
June–August
Sukumo (dye) production:
November–February

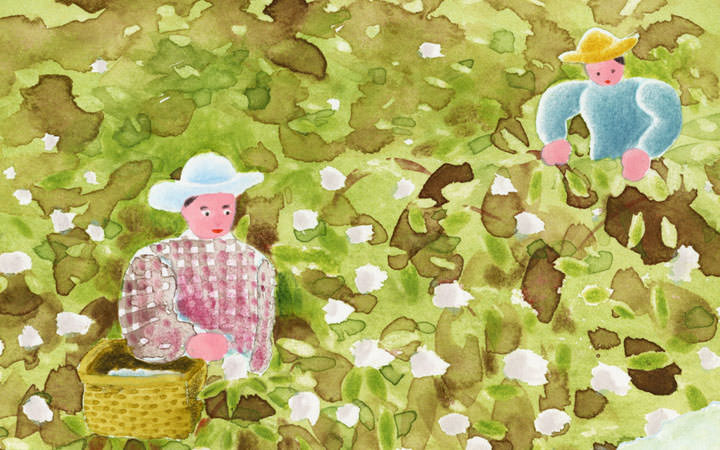
Raw cotton
Zimbabwe cotton and Supima organic cotton are two
essential pillars of our enterprise.
Zimbabwe cotton
soaks up the brilliant African sun as it grows. It has
firmness and body, and brims with energy. It makes fabric
with a crisp, dry feel that conforms more snugly to your
body with every wash-wear cycle.
Supima organic
cotton is soft and supple, with extremely long fibers that
are a true rarity and impart a refined gloss. The elegant
feel of Supima organic cotton textiles is truly unique.
If you want to make clothes that feel good, nothing
is more important than your raw materials.


Spinning Yarn
Spinning yarn is another task we put our own spin on. When making yarn for T-shirts and denim, we make a point of creating slight variations along the yarn’s width. This gives the fabric an uneven surface that almost seems to be laughing. This is the secret to making garments that feel fresh and don’t cling to the skin.
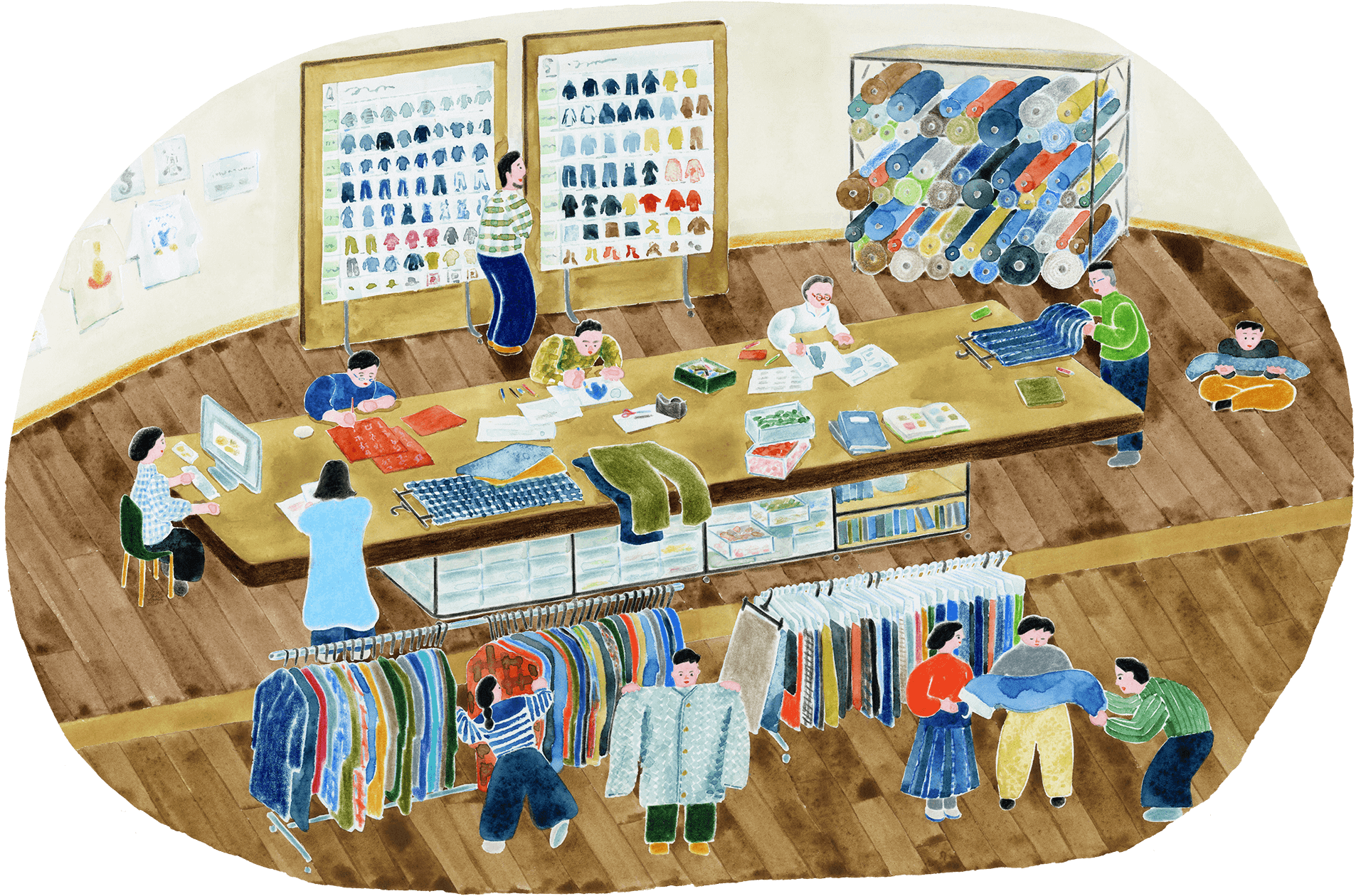

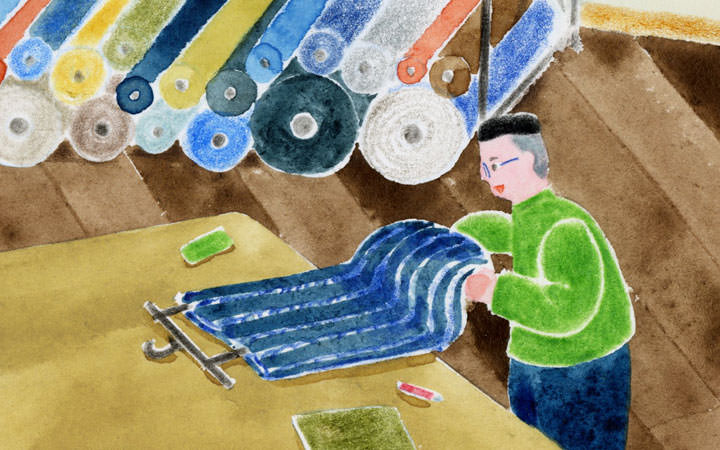
The Human Touch
To make the clothes we want to, nai monozukuri is the only way. Our basic approach is to choose the raw materials and make everything ourselves, from yarn onward. As we work, we use our hands to touch, to feel, to press the fabric to our skin and make sure it feels as good as we imagine. Step by step, we bring garments into being that have never existed before.


Yasumi-san
Yasumi-san’s family owned a kimono store in Hiroshima
Prefecture. She loved to draw from a young age, and she
also loved fashion so much that she would naturally study
it in movies, in photographs, and simply out
peoplewatching.
Even now, Yasumi-san’s head is
constantly filled with new ideas—unique designs and styles
that she gets down on paper in sketches.
Incidentally, these are her favorite glasses, which
she wears only at work.

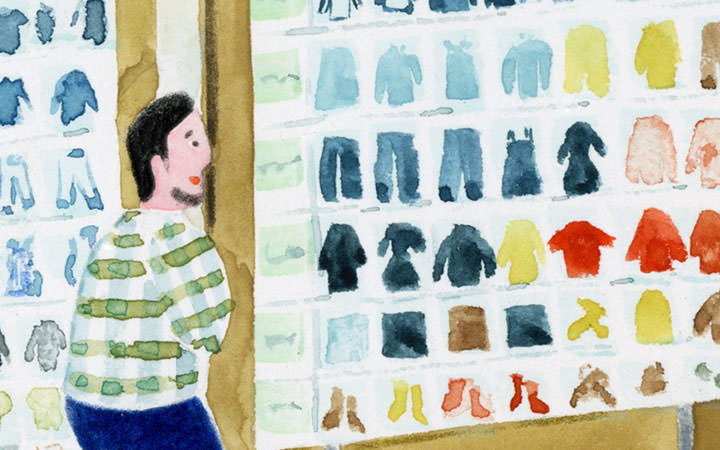
Folding in Stories
What we prize is clothing with stories.
That story
might be about a solitary woman, a place, a photograph . .
. Whatever the case, we plan our approach to design based
on that story. Would an oversized sweater suit that
character? What about a skirt like this . . . ?


Graphics
All of our designs are drawn by hand, from T-shirt and
fleece prints to intricate floral and paisley patterns for
blouses and bandanas.
Look closely at hand-drawn
designs, and you can always see a certain cheerful
irregularity. That sense of play is what gives our clothes
their “45R-ness.”

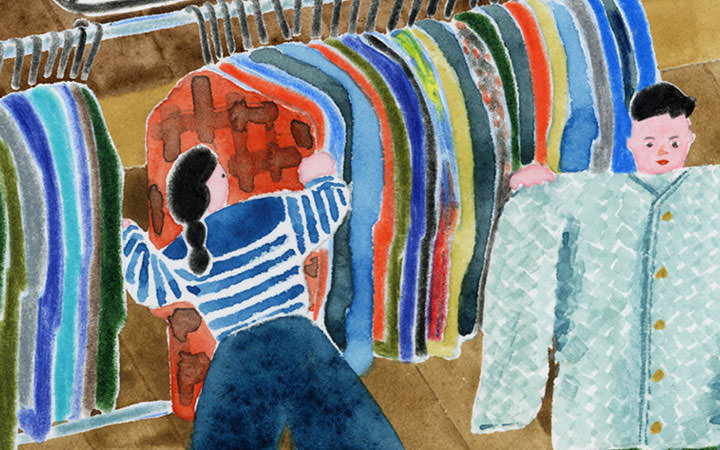
Vintage Gallery
Our vintage gallery has rack upon rack filled with vintage clothes collected from the United States, Europe, and Asia. Some of our pieces are so rare they’d be difficult to find at a retail vintage clothes dealer! This is a treasure trove of ideas for monozukuri.

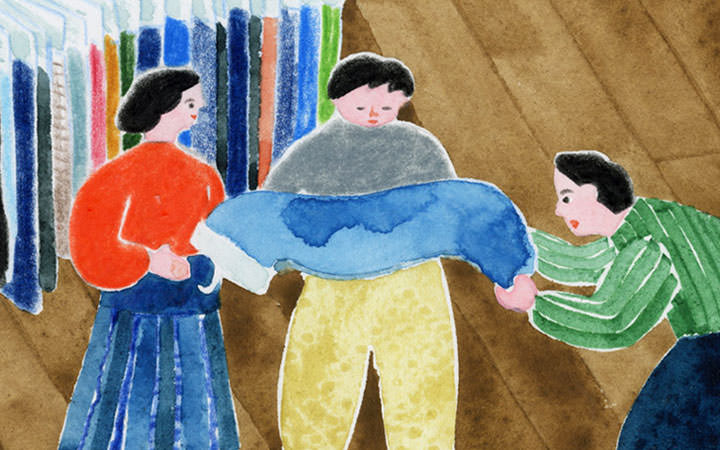
Down to the Last Floorcloth
In days gone by, there were no handy machines or
artificial fibers. The clothes people made had to be
richly functional, born of the wisdom of handcraft and
pride in a job well done. Garments were handed down as
people outgrew them, and when they finally got too old to
use, they were cut up and resewn into quilted floorcloths
to use some more.
We look very closely at the
textiles we encounter—how individual threads are
organized, how the sewing is accomplished—and use this
information in our work. There’s so much we can learn from
those who came before us. Their culture of letting nothing
go to waste is an inheritance we prize.

Breathing Life
Into Material
The Katachi Research Department—katachi is Japanese for “shape” or “form”—is divided into two teams: Modelists (patterners) and Dandori (production managers). Together, they give ideas form. Somewhere inside 45R, in a room with “LABORATORY” written on the door, Modelists in white coats busily work the treadles of sewing machines. (There are more than ten sewing machines in the laboratory, each designed for a specific kind of work.) Modelists do more than simply create paper patterns—they are tailors in their own right, who can and do make the finished garments those patterns represent. What our Modelists strive to uphold is, in a way, the art of not designing. If you gaze at a textile and ponder its practical applications long enough, the most beautiful forms it could take on eventually present themselves. Simple beauty is found in function.
Once a new garment’s form is finalized, the next step is turning this into a product that can be produced in bulk. This is where the Dandori take over, taking samples made by the Modelists along with very carefully written specification sheets to our factories to discuss production. Dandori keep their hands on the tiller until the product reaches store shelves. From Koromo Research Department to factories, and then to stores—our Katachi Research Department connects people to each other and to each other’s passion. Its team is the fulcrum of our monozukuri.


Modelists
Modelists bring fabric to life, searching for the forms
and specifications that suit each textile best. They
pursue design born of function, like those seen in vintage
garments that have been worn with love for years. And they
do this because they understand the value of going the
extra mile to express something beyond imitation—something
real.
All without forgetting their sense of fun, of
course!
Ura koso omote: “What is hidden from view is
a product’s true face.” This is the idea that guides our
Modelists as they strive to create patterns they would be
just as proud of if they were taken apart and scrutinized
a hundred years from now.

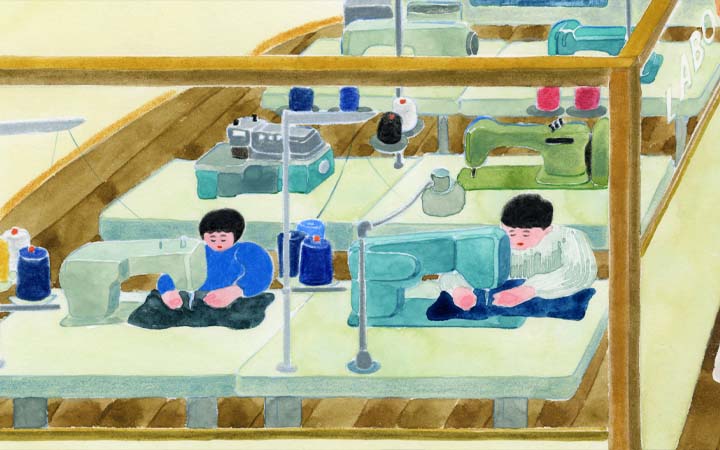
Toile fitting
Once the pattern is ready, the first toile is created.
This is an initial version of the garment made using the
pattern but out of plain sheeting rather than the actual
intended material. The goal at this stage is simply to
check the form.
Modelists make their own toiles using
our laboratory’s sewing machines. Piecing the shapes
together with their own hands helps them identify any
issues with the specifications or form they have
envisaged. The toile fitting is also used to pick out
issues that only reveal themselves when the garment is
worn by someone.
After repeated cycles of making,
unmaking, and remaking, the Modelist finally arrives at a
design that satisfies their expectations.


Sample Racks
Once we receive the final samples from our factories, we
carry them to the exhibition hall for display.
A hall
full of samples lined up in rows is a breathtaking sight.
What kind of story is about to begin? This is a moment of
pure excitement for everyone involved, from creators to
store staff.

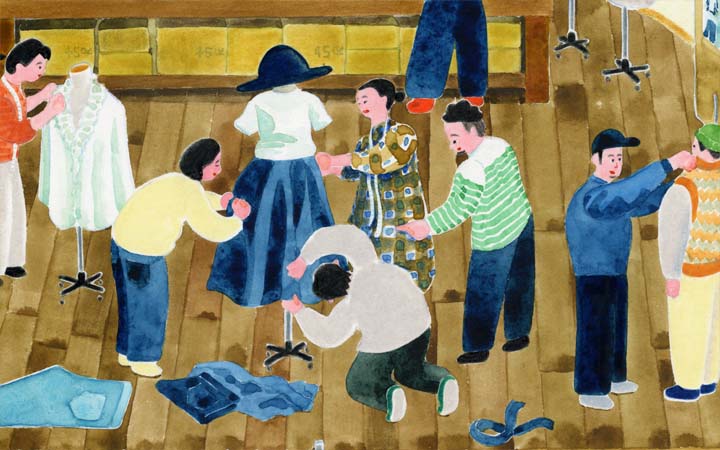
Actual Size, Actual Materials
The Katachi Research Department takes fabrics fresh from
the Koromo Research Department and tailors them into
sample garments. Because we do our own prototyping, we are
able to create detailed instructions and identify points
where caution is needed, and these are shared with our
factories. We make our own buttons and fasteners as well,
so confirming their compatibility with the fabric is
another key task.
Once the sample is sewn together,
we ask: Does it work as we envisaged it? Did we design it
in the right size? At this stage, adjustments are often
made by the millimeter.


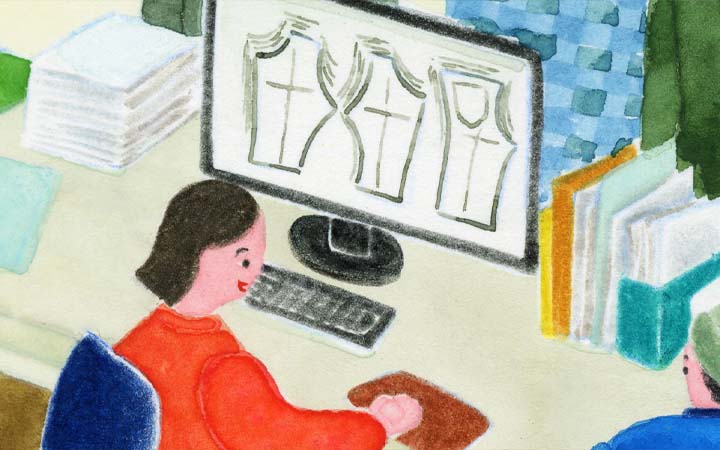
Grading
Our clothes can be enjoyed in a diversity of ways, from
small to large, so sizing is crucial. Working from the
sample as a base size, we change the pitch and scale the
pattern up and down as needed.
This doesn’t just
mean changing measurements. Different sizes require all
kinds of specialized grading. Pockets need to be
repositioned to maintain balance, and even the size of the
stitches can differ. The goal is simple:
to ensure
that every garment in every size is as cute as it can
possibly be.


Shokudashi
“Eight parts preparation, two parts execution,” as an old
Japanese saying goes. Shokudashi literally means “Sending
work to the artisans.” This is the process that brings the
ideas from our atelier into the world at large,
transforming one-of-a-kind samples made with as much care
as any folk craft into products we can sell at stores
around the world.
As we hand the baton to our
factories, we always keep one thing in mind: No matter how
many of a given product we make, for the customer who buys
it, it is their only one.

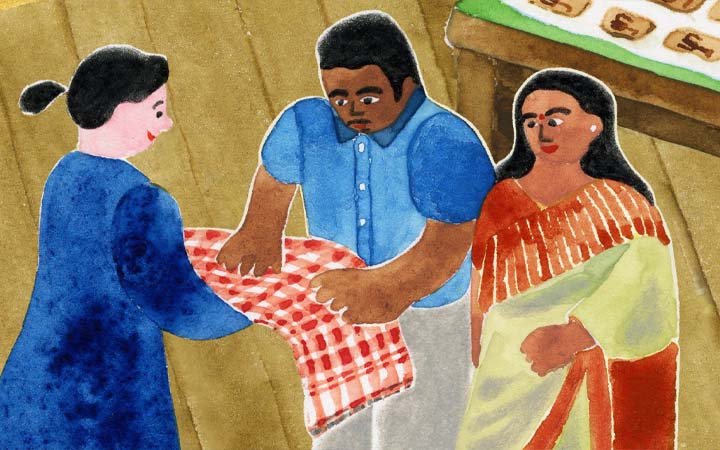
Partners Around the World
As part of our search for the truly unique—things that
can’t be made anywhere else, or by anyone else—we aim to
create a worldwide network of specialists connected by our
roots.
“Made in Japan” is important to us, but above
all we are driven by our passion for nai monozukuri—making
things that do not yet exist, but should. Unbounded by
language or culture, with our sights set high, we
communicate in the common language of passion.

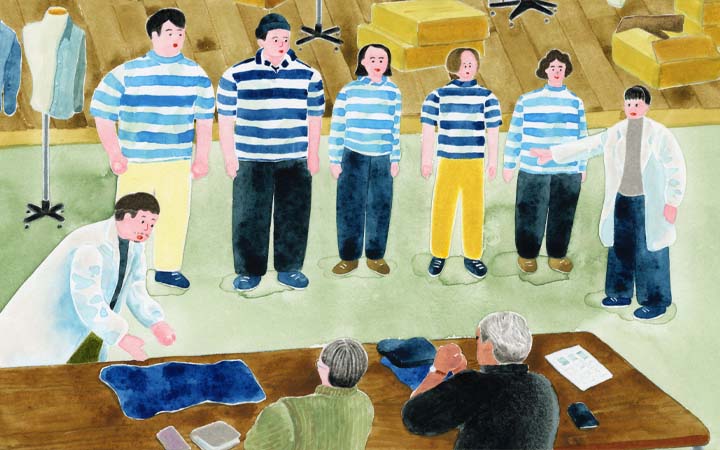
The Final Check
An electric atmosphere. Lines of models wearing new
garments, awaiting inspection.
This is the final
check, where everything is examined closely: materials,
shape, silhouette, delivery date, and the finest details
of the specifications. The sharp eyes of our Oyakata (also
the company president) examine garments from the front,
sides, rear, and even the inside. All so that that we can
enrich your daily living by offering “feel-good”
clothes.
We make our clothes with passion and with
care. Examining the finished product anew from a fresh,
bird’s-eye perspective is the vital final stage in the
process.
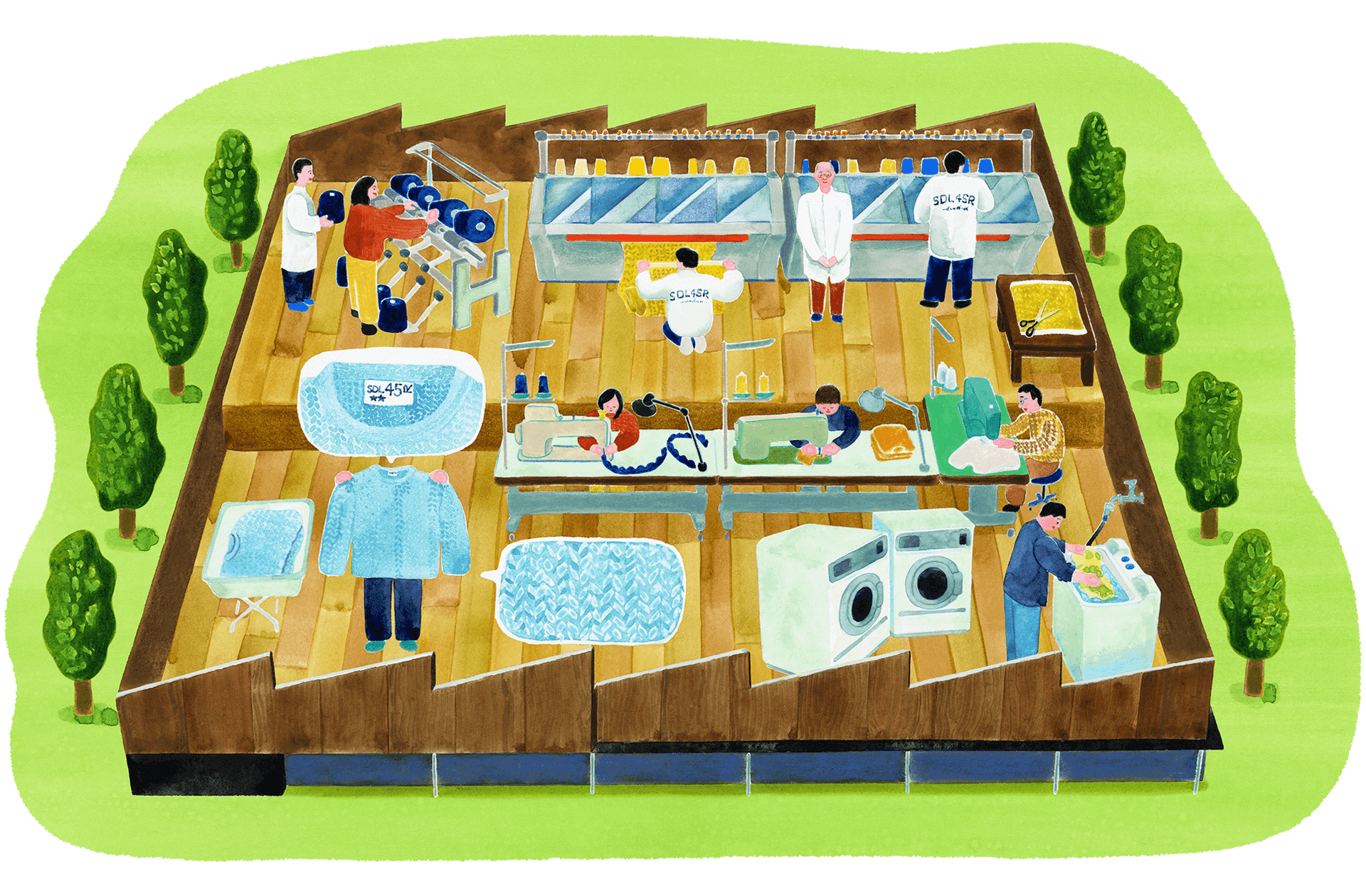
Feet on the Ground,
Working With Our Hands
There aren’t many clothing companies that also own their own factories. Ours began as a partner we met through our president, and eventually joined the 45R family directly. The sweatshirts our sweater factory makes have a puffy volume to them that you won’t find anywhere else. A few years from now, the factory will move to Ichinomiya, and a new history will begin.

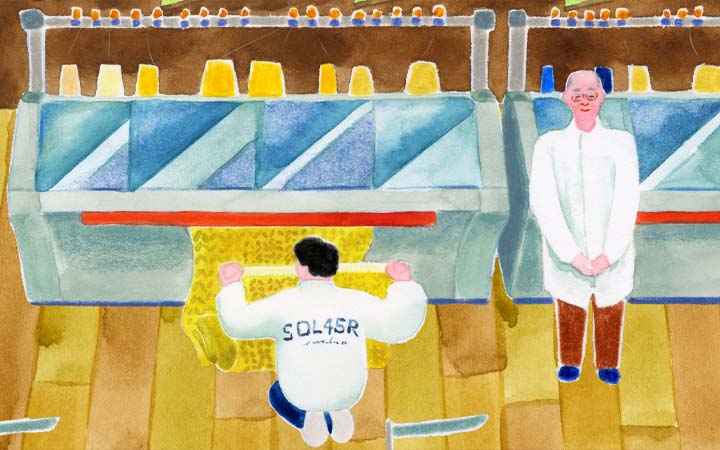
Knitting
SDL 45R has venerable old knitting machines whose sound
and movements have a nostalgic leisure to them—like a
steam train. They produce fabrics with a certain
irregularity to them here and there, adding depth and
allowing an air-filled puffy finish.
Taking this as a
starting point, SDL 45R is now sharing its techniques with
a new generation of artisans, striving busily every day to
bring feel-good knits to customers around the world.


Sewing
Knitted fabrics are sent through SDL 45R’s in-house
washing machine, where the water adds character. Then they
are carefully cut, and the pieces sewn together.
Prickly
seams can undermine the best-feeling fabric, so we sew as
smoothly as possible, keeping the wearer foremost in mind.

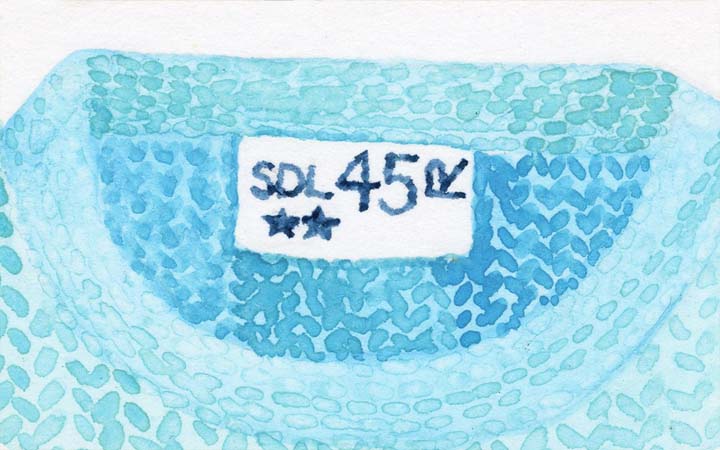
Made in SDL
Clothes made at SDL 45R proudly bear witness to that
fact.
Each garment has its own name tag—a tube of
knitted fabric with “SDL 45R” embroidered on it in red
thread.
Tags are part of clothing. They have to suit
our soft, high-volume knit-and-sew garments.


A Repository of Technique Headquarters
SDL 45R’s strength is its mastery of a wide range of techniques, from knitting to washing to sewing. Normally, each of these tasks would be handled at a separate factory. The knit-and-sew garments they produce combine all of these techniques into individual garments that break the mold of monozukuri. There’s a reason they can’t be found anywhere else: only SDL 45R’s techniques make them possible.
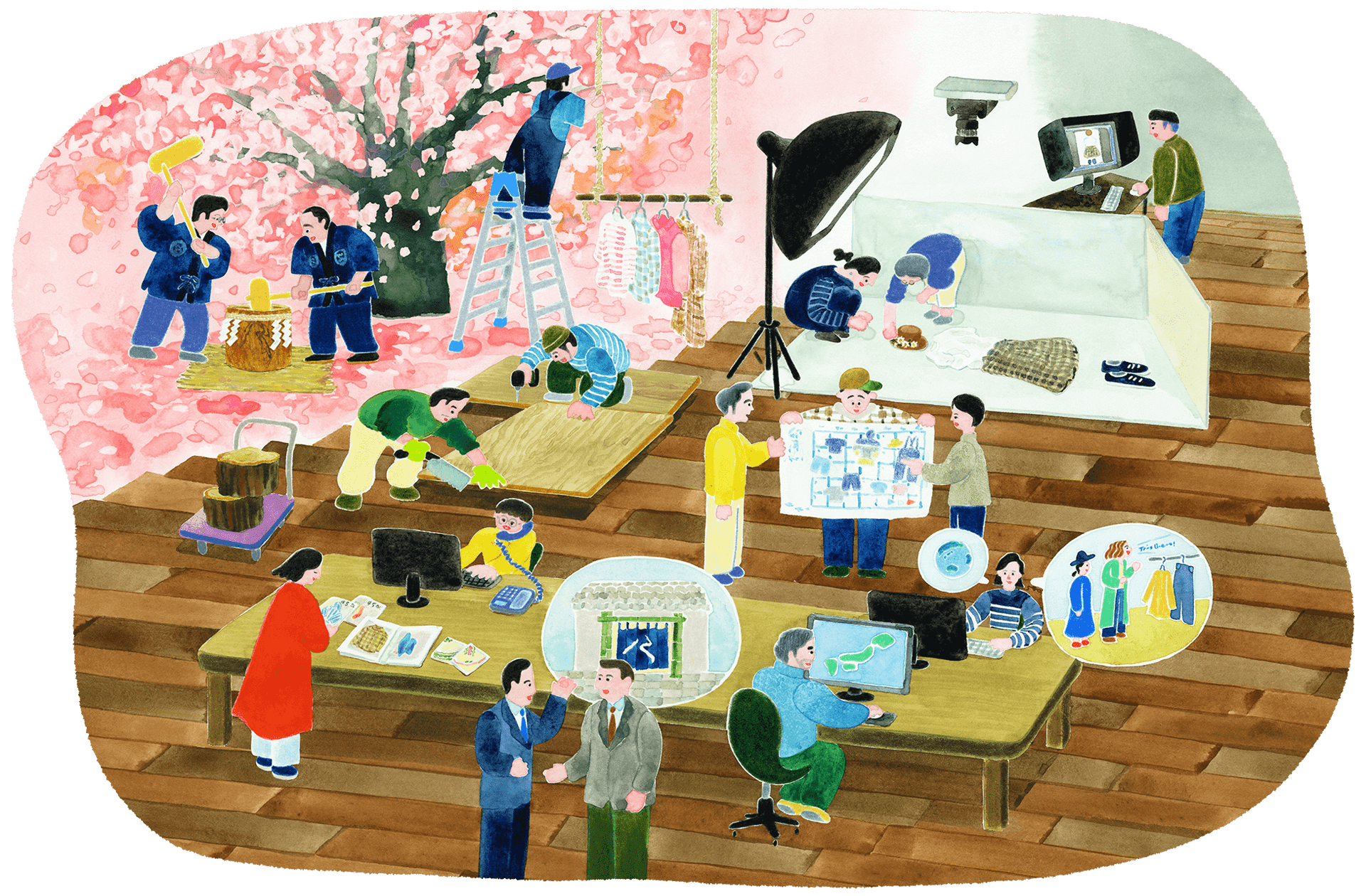
Fully Focused on
Delivering Delight
Appare is Japanese for “Glorious!” or “Well done!” The Appare Department’s mission is twofold: to fill stores with 45R products and the passion of those who make them, and to continue delighting customers with any additional support needed afterward. Any homare (praise) or “Seeds for growth” (customer comments) we receive are fed back into future monozukuri and customer service, creating new virtuous circles. We call this an iyasaka no kairo—a circuit in which everything keeps getting better and better. Whatever challenges we face, the Appare Department strives to keep glorious flowers blooming.


Masters of the Seasonal Calendar
“This is adorable! They’ll love it! Make XXXX copies—no,
more!”
What to print, and how many copies; when to
lay it out in stores . . . Discussing these questions is
the Merchandising team’s job. We prepare estimates and
plans with the goal of reaching as many customers as
possible with zero waste, assembling the 45R of tomorrow.

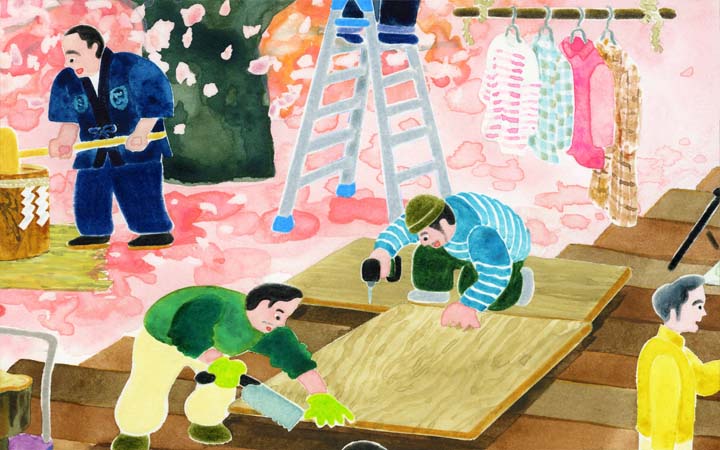
Furnishings
Tap, tap. Vrrr, vrrr. Several times a year, these sounds
echo throughout our atelier as we prepare for an
exhibition by making our own “furnishings” (shitsurae—our
term for visual merchandising).
Our passion for
monozukuri is expressed not only in the clothing we make,
but also the work we do to breathe life into exhibition
spaces. We then recreate these spaces faithfully in our
stores and welcome customers into them every day.


Catalog Design
We start each season with a catalog that reaches customers
just before our garments do. Designer Yasumi Inoue takes
the lead in finding new ways to share the worldview in our
minds with the world outside.
The more pages you
turn, the more pleasures you find. We strive to make each
catalog the kind of publication that demands to be shelved
and kept no matter how old it gets.

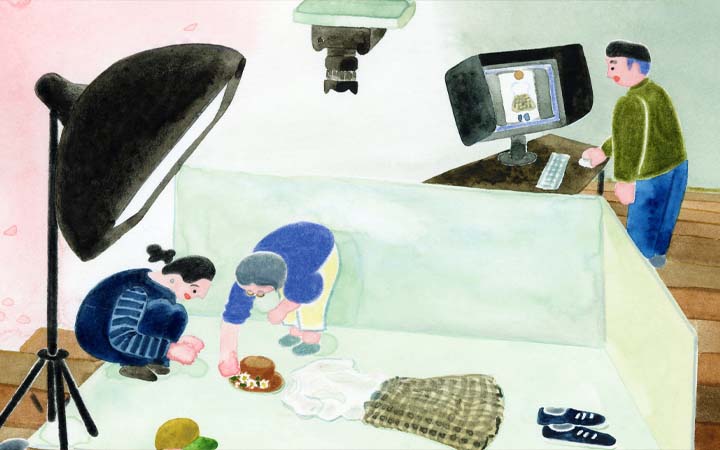
Outreach
In order to share the passion of the workers behind our
clothes directly, we started sharing a range of
information through social media and our website, with a
rapidity and closeness that feels “close enough to share
soup.”
As part of these efforts, we shoot video
productions in our atelier, from 45R Blue Ocean Movie, a
monozukuri movie produced by actual planning staff, to
Yasumi Inoue’s styling suggestions or “Yasuminates,” which
she has been offering for 30 years.
We also handle
press, including putting samples in stylists’ hands.


Goyo-kiki (Listening)
“Well, this is a problem . . . What should I do now?” At
times like this, please contact the Listening team!
Our
mission is to listen to and understand customers that
contact us in a range of ways, from email to telephone,
and to resolve their issues as quickly as possible.
But
that’s not all. The Listening team also plays an important
role by using this feedback as “Seeds for growth” and
performing course corrections to fine-tune 45R’s circuits
for even better results.

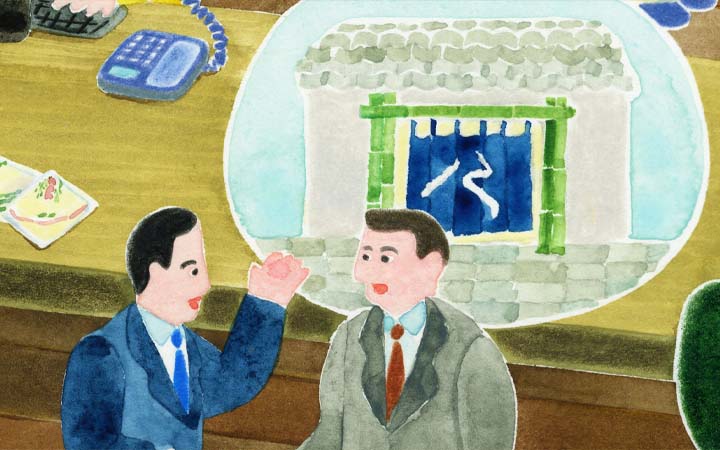
Minding the Store
“Sanpo-yoshi”—good for buyer, seller, and society—was the
traditional business philosophy of the famous Omi
merchants of Japan. We strive to follow their example by
initiating and maintaining positive iyasaka no kairo
circuits that benefit artisans, customers, and regional
communities.
To run a store that feels good,
cooperation from department stores and our fellow tenants
is essential. We share information and craft marketing
plans to ensure that we approach things with the same
aspirations.
For new stores, the process is the
same. We hold discussions with local stakeholders to make
sure we make our arrival in a manner that works for
everyone.


Inventory Management
We create accurate sorting orders to send products gathered from workshops to stores around the world. Our inventory management efforts cover not only products but also the business supplies used by 45R stores, which we order and ship as needed. We are the head stocktakers of the Appare Department.


International Store Management
45R has stores in the United States, France, and many cities in Asia.
Our job is to make sure that the passion for monozukuri that begins in our
atelier reaches customers along with our products, no
matter which store those customers visit.
We help
overcome the language barrier at exhibitions, handle
trans-oceanic shipping, and run training sessions for
staff from different cultures. We want to share 45R with
as many people as we can, and that means eagerly
connecting with overseas customers we haven’t yet met—but
soon will.
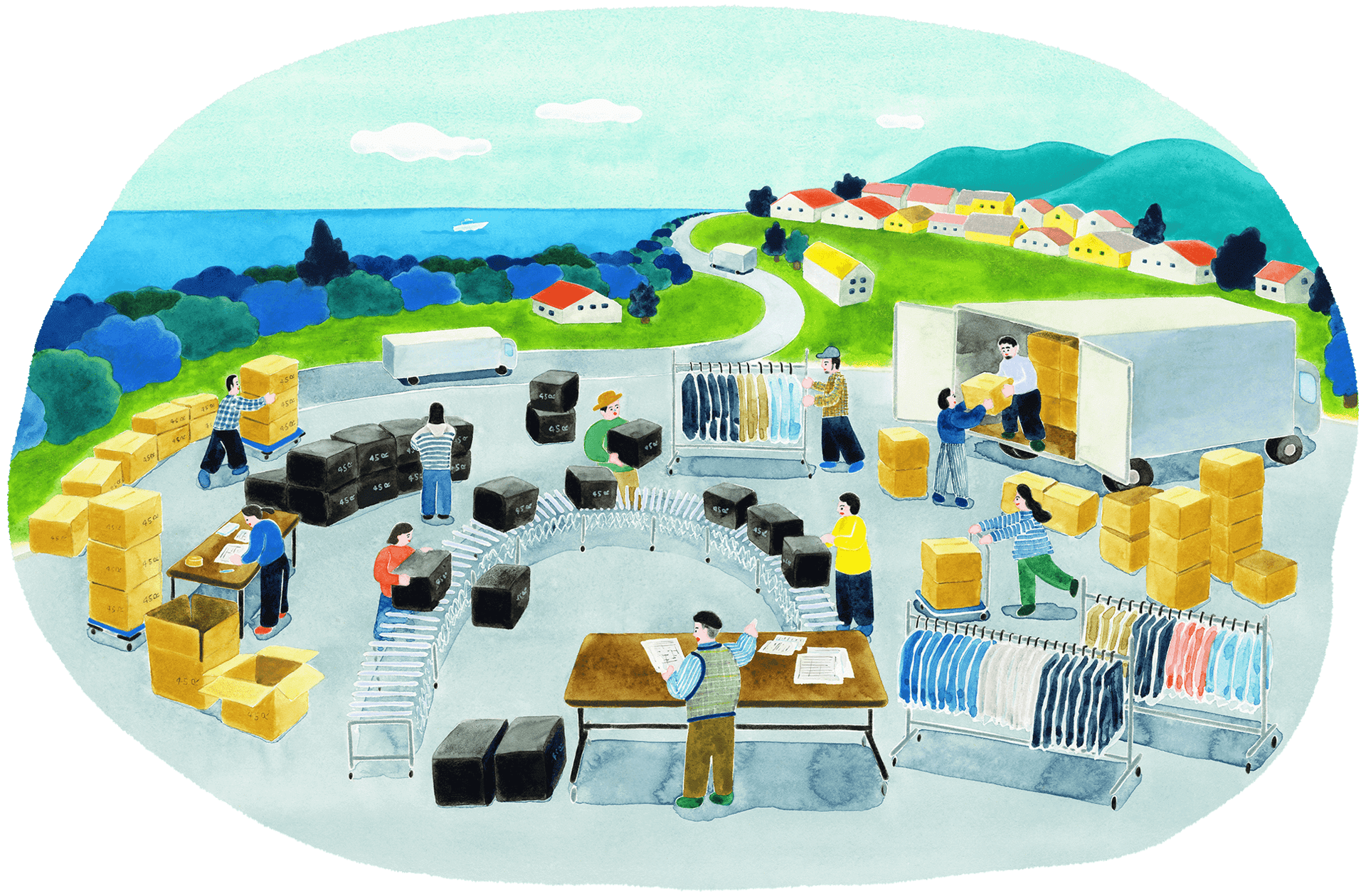
Soft Clothes,
Boundless Passion
Our internal distribution center 45 Studio R sends our products, which are made with love and care, to stores around the world. Each item is packed lightly in its own box to avoid creasing, and sent on its way with a cheerful “Safe travels!”
We could have the most appealing lineup, the most stylish stores, the most wonderful staff in the world, but none of it would matter if the clothes stopped circulating. 45 Studio R is the beating heart of everything we do.

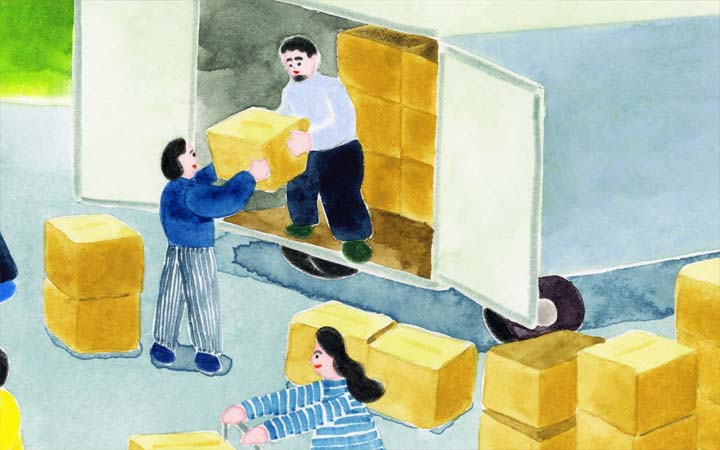
Receiving and Inspection
Freshly made clothing arrives not just from Japan but from
factories around the world.
“What’s in the shipment
today?”—the 45 Studio R staff open the boxes with
excitement, as if they were treasure chests.


Sorting and Shipping
Products are packed in individual boxes for shipment to stores. This helps keep them soft and fresh. To avoid creasing, we make sure to leave just a little more space than necessary.

Our Stores,
Ourselves
Two things make a store: its staff and its furnishings. At 45R, we want both of these to be bright, fresh, and individual. We believe this builds the store’s value, and we work on ourselves to that end. Not just by learning more about our products, but also by learning how to style them, furnishing our stores appropriately, studying customer service, and even taking tea ceremony lessons!
We go beyond the framework of the store to learn together autonomously, cultivate individuality, and put this to use in everyday life. This means that when it’s time for work, 45R’s stores are always filled with energy and smiles, and we can welcome customers into an invigorating and healthy space.

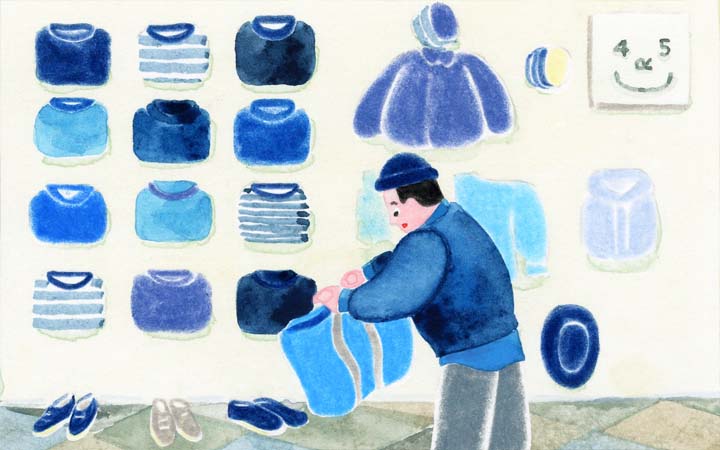
Adorning the Store
“Fluffy as fresh-baked bread.”
45R’s products are
created with attention paid to the tiniest detail, and we
arrange them in stores carefully to ensure that customers
see each item at its best. We also use steamers to make
clothes soft and fluffy without a single wrinkle.
Our study sessions about products and point-of-sale
design help staff keep all merchandise on display with the
most appealing points clearly visible.

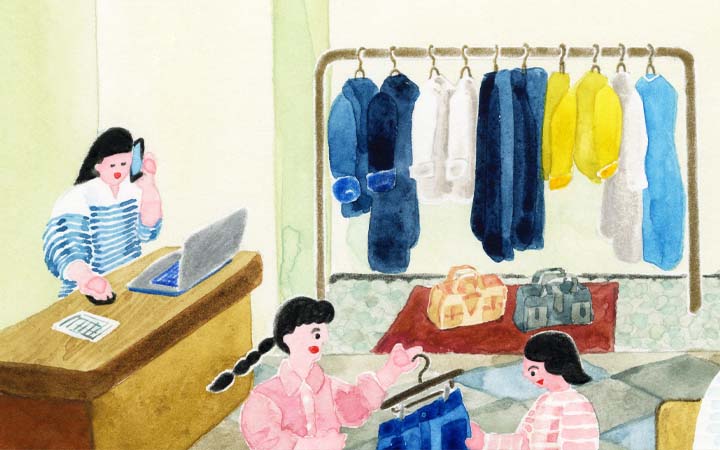
Ordering
Each 45R store stocks a different selection of
merchandise. The reason for this is simple: at our
seasonal exhibitions, each store manager decides what to
order for their store.
We believe that the staff at
each store know their business and their customer base
better than anyone at headquarters. Managers take
responsibility for deciding what they can sell—down to the
very last piece.


Observant Eyes, Thoughtful Minds, Caring Hearts
We are missionaries of emotion, conveying the thoughts
included in 45R’s products to the customers that buy them.
We use the latest information to help those customers bond
with their new purchases in a way that suits them.
Our LINE account is a low-pressure way for customers
to reach us; our telephone support lets customers explain
things in a relaxed fashion; our seasonal missives and
Instagram posts share information for customers to peruse
at their leisure. In all of these media, we strive for the
quality of one-on-one interaction.

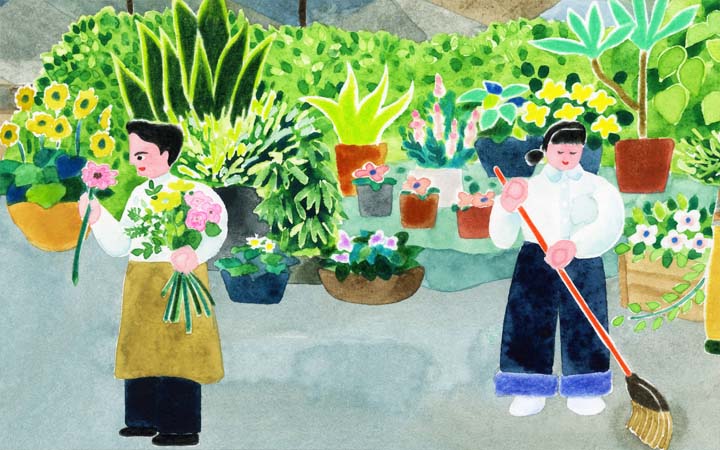
Hanadokoro Edozakura Florist
More than a few of 45R’s products were inspired by the
elegant shapes and colors of nature. Flowers that may not
be flashy but are tiny and adorable, plants with
appealingly off-beat forms—our Hanadokoro Edozakura
florist deals in a wide range of flowers we fell in love
with at wholesale markets.
Delivering the delights of
each season to our customers’ everyday lives is our
pleasure.

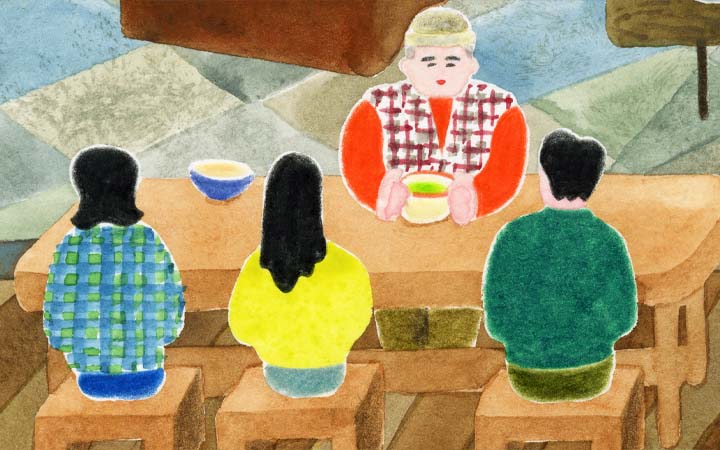
Tokowa/kairo: Lessons in Grace
By studying traditional Japanese rules of civility and
etiquette, we can take the hospitality we offer customers
to the next level. Leaping outside the company to learn
under the watchful gaze of a cheerful chanoyu teacher is
our Tea Ceremony Club.
Everything this tokowa/kairo
learns can be used in stores, from enjoying the changing
seasons to treating utensils and equipment with care. And
every so often, we hold tea gatherings in a special tea
room at our Badou-R headquarters.

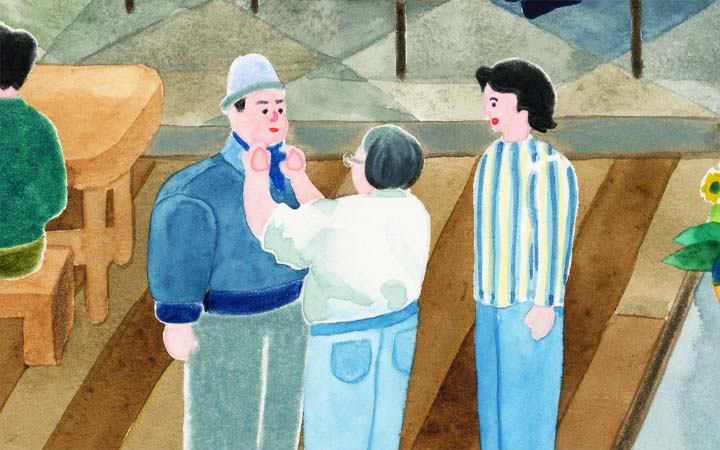
Tokowa/kairo: Styling Sessions
Tokowaka means perpetual youth and freshness. Our
tokowa/kairo or “tokowaka circuits” are organizations that
revolve around our in-store employees, designed to help
them continue developing as people without getting rusty.
Teams operate across store and geographical boundaries in
a variety of fields.
These activities include study
sessions on styling, where members learn to choose and
wear outfits in a way that is true to both 45R and
themselves.
After all, we sell clothing—we have to
look good!



Online Store
“Welcome to the store!” when arriving at work; “Thank you
for visiting!” when leaving for the day—45R’s online store
staff make their greetings to the computer screen.
They
may not meet customers directly, but they are proud to
operate a store that customers can shop at freely, anytime
and from anywhere that their lifestyle makes convenient.

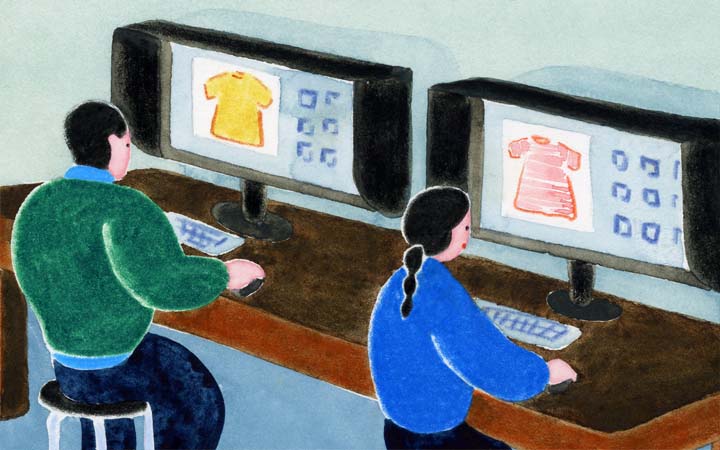
Photography and Storytelling
“Take a look at this!” “Let me show you why this material
looks so cute!”
Our staff find ways to showcase the
myriad tiny details 45R focus on when making clothes,
creating a conversation through photography. They see and
wear and touch the garments in place of customers, and
then turn those experiences into words, weaving in the
passion of the artisans and the monozukuri background—just
as if they were writing personal letters.


Inventory Management
Our online store has the widest range of any of our
outlets—3,000 different products in all! Inventory is in
constant motion, with new products arriving and being sent
to other stores by the day.
To ensure that none of
this bothers our customers, we manage our stock strictly,
down to the last item. We also perform careful quality
checks, to make sure that nothing disappoints when it
reaches customers’ hands. We even make sure to keep indigo
out of the sun to avoid premature fading, while still
keeping it ready to ship at any time.

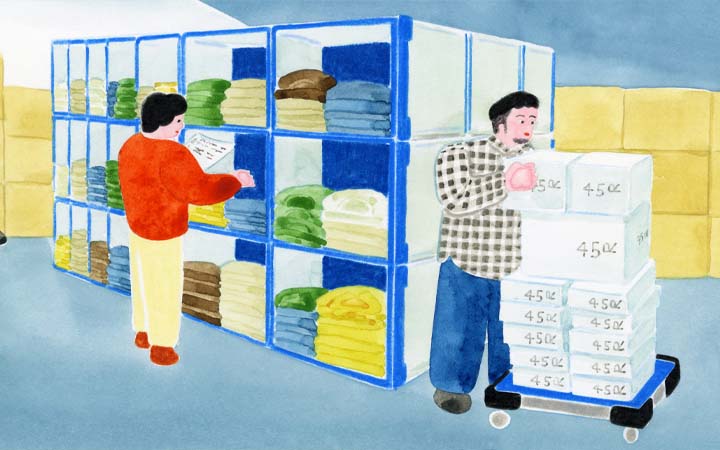
Pickup and Shipping
Imagine a wall lined with clothing. Our whole staff helps take garments down from the wall and prepare lots for shipping, to make sure the job gets done quickly but without any color or sizing problems. We carefully refold each garment, imagining how excited customers will be to see their orders when they open the boxes. Once the boxes are sealed and ready to go, we wish them a hearty “Safe journey!” and track them carefully until they arrive safely at their destination.
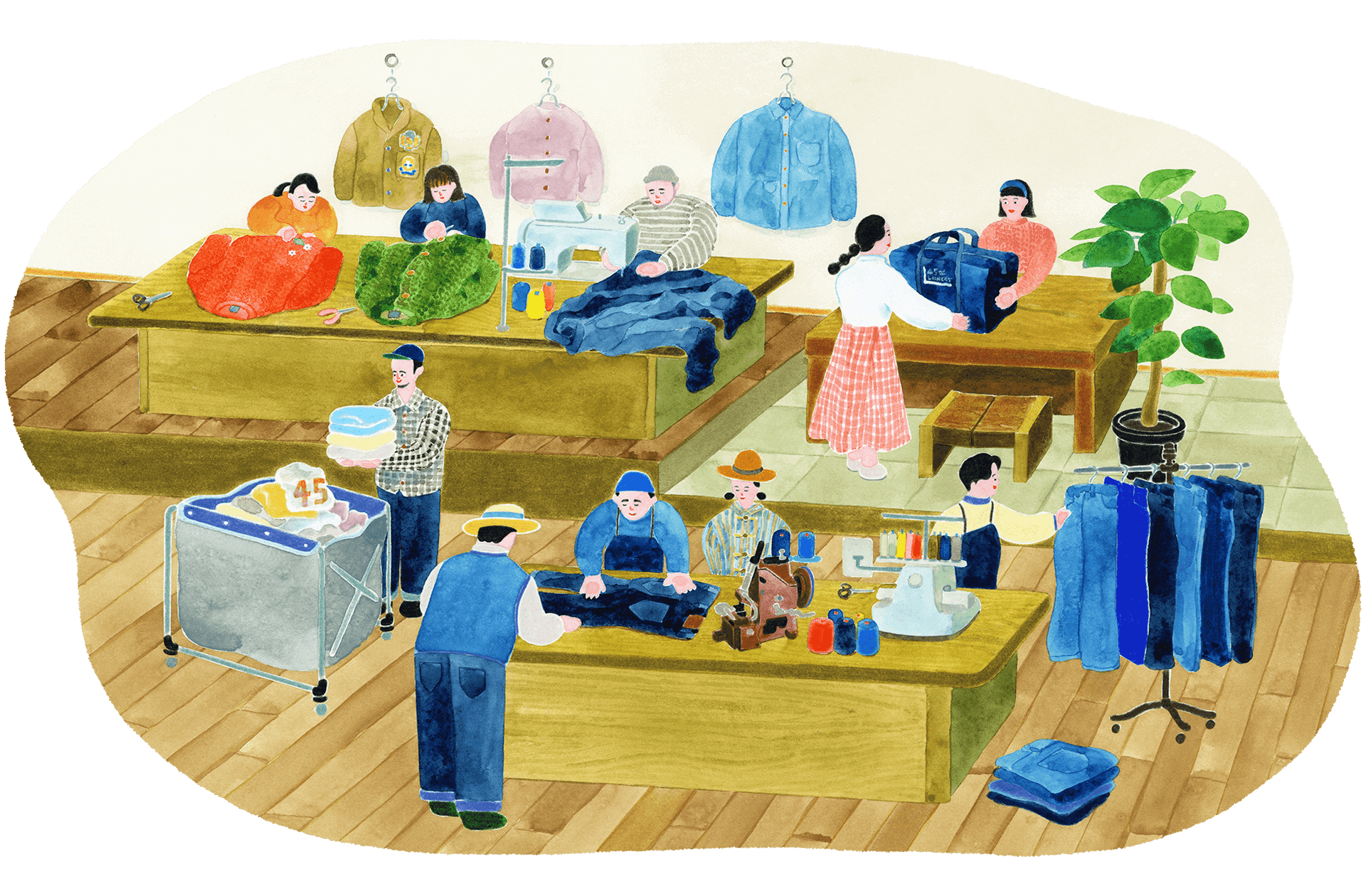
The End?
No, the Beginning!
45R’s relationship with a customer doesn’t end when they buy one of our products. In fact, that’s when the relationship begins! Our service team is dedicated to helping customers enjoy the clothes they decided to buy for as long as possible.
Our Manzoku Atelier offers everything from alterations to complete remakes. The 45R Laundry refreshes garments that need a pick-me-up after a hard season’s work. Futatabi Jeans breathes new life into denim that is no longer worn. The service team honors the love our customers feel for the garments they chose to buy, delivering satisfaction and joy.

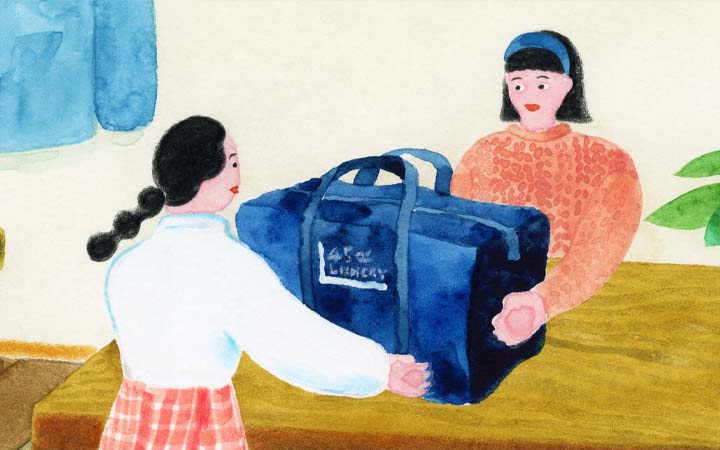
45R Laundry
Proper care is vital for clothes in heavy rotation.
We
work with dry cleaners whose techniques are friendly to
both humans and the environment to restore clothes to a
state that feels good while preserving the character they
have developed. Naturally, we take responsibility for our
customers’ precious garments from the moment we accept
them to the moment we give them back.


Satisfaction Workshop
“I don’t wear this anymore, but I can’t bring myself to
throw it out . . .”
“I wore this so much that it’s
full of holes now . . .”
“This is a little bit too
long . . .”
These are the issues our Satisfaction
Workshop resolves, mending and remaking clothes to breathe
new life into them.
Sometimes we hold a pop-up
Satisfaction Workshop in one of our stores, and the
classic items brought in by customers reflect years of
love! We accept responsibility for keeping this love alive
by ushering those garments through the process of rebirth.

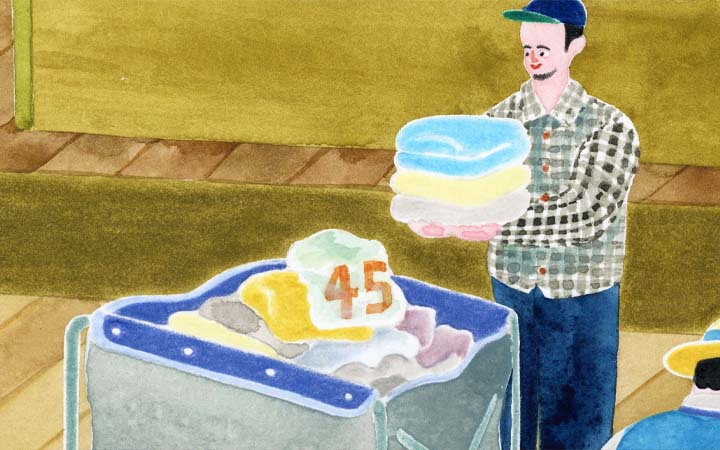
Futatabi (Recycling)
We value clothes and avoid waste.
To keep unnecessary
disposal to a minimum, we accept clothing that has
finished serving customers, reclaim its materials, and use
these to make new garments.
Heed our call, O garments
of 45R!


Futatabi Jeans
45R is a denim brand.
Denim can show many different
faces depending on who wears it. That’s part of the
appeal! But sometimes it can be hard to “raise” denim the
way you imagined . . .
Futatabi Jeans—futatabi means
“again”—accepts these wayward garments packed away at the
back of customers’ closets, and applies processing and
color alterations to give them a fresh new look.
Then you can start “raising” it into a one-of-a-kind
item all your own once more.

Monozukuri Is
More Than Just Monozukuri
“To be an institution, you have to do more than just uphold tradition. We are living in the present, and evolution and innovation are our mission.” This idea is one of our starting points, and the team at our Ometsuke Department—ometsuke meaning “management” or “supervision”—are the unsung heroes that make our work possible. Behind the scenes, they keep 45R humming by handling personnel, general affairs, and accounting.
The Ometsuke Department’s Personnel and General Affairs staff are responsible for creating a workplace where employees feel safe, secure, ready to work, and able to grow. Our employees come from many different generations and walks of life, but the department’s staff connect with each and every one as an individual. Meanwhile, the Accounting staff hold the company’s purse strings, keeping a strict eye on the money that flows in and out from day to day. This strictness is, of course, for the benefit of the company and its staff. We’re proud of our taut, muscular accounting approach, which combines evolution with innovation.

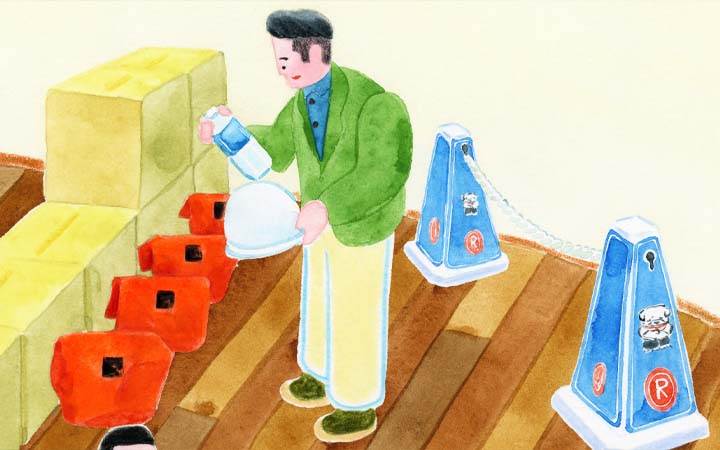
Disaster Prevention and Security
If disaster should strike during the work day, we have all the equipment we need on hand for employees to seek temporary shelter. We maintain and manage it carefully to make sure nothing is missing or unusable should it be needed. And, to protect the company from danger on a more everyday level, our maintenance and security efforts are airtight.

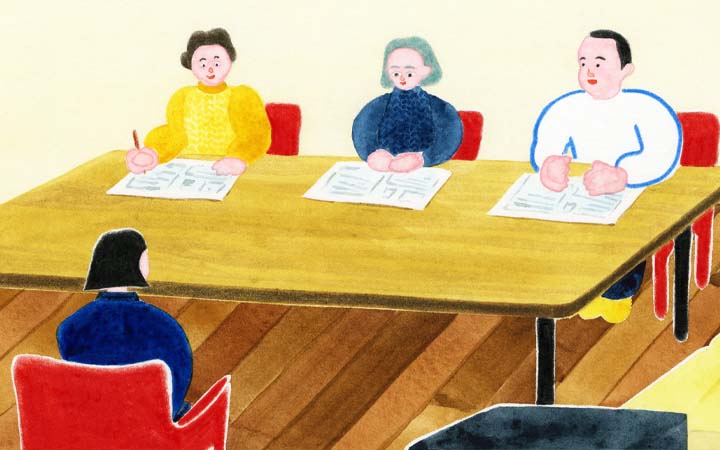
Personnel and General Affairs
Our Personnel and General Affairs team finds people who
identify with our feelings about clothing and want to pour
their passion into working with us. You might say their
job is to uncover and polish diamonds in the rough. They
also maintain a working environment that lets employees
focus on their own work, and create administrative systems
that let staff and their families lead healthy lifestyles.
Working while raising children is the norm today,
and our Akane Team is made up of working parents who come
together to support each other.


Systems and Infrastructure Maintenance
Much of our work is still done by hand in the analogue world, but our IT systems are the fulcrum of the company. Our Systems and Infrastructure Maintenance staff perform a wide range of development and maintenance tasks to bring 45R together as a unified organization, from setting up company phones to designing and constructing mission-critical backbone systems.

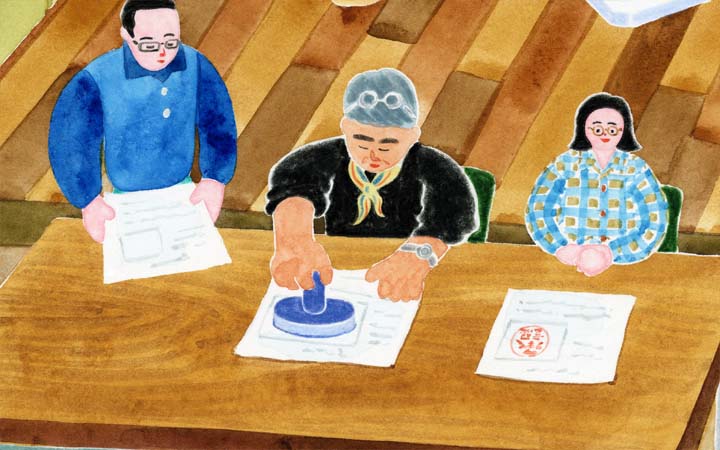
Finance and Accounting
Monozukuri, hitozukuri (training people), misezukuri
(building stores), kaishazukuri (growing the company)—to
ensure that all of these go smoothly, our accounting staff
keep a close eye on our figures every day.
As a
general rule, they use IT systems for their work, but the
final step is analogue—finalizing their decisions with a
large stamp that reads “APPROVED.”
This is their
morning routine as they support the company with our
Oyakata, like runners in a three-legged race.